Packaging Machine Repair Service: Guaranteeing Marginal Downtime and Maximum Effectiveness
Packaging Machine Repair Service: Guaranteeing Marginal Downtime and Maximum Effectiveness
Blog Article
Recognizing the Secret Components and Repair Approaches for Product Packaging Maker Maintenance
Effective upkeep of packaging machines pivots on a thorough understanding of their vital elements, including the structure, drive system, and sealing mechanisms. Identifying typical upkeep problems, coupled with the execution of preventative techniques and troubleshooting strategies, can substantially enhance machine integrity. The selection of fixing techniques, including the usage of OEM components and the significance of qualified specialists, plays a critical role in minimizing downtime. To absolutely grasp the ins and outs of these systems and their upkeep, one must consider the more comprehensive ramifications of overlooking these necessary techniques.
Key Components of Packaging Machines
Packaging machines contain several key parts that collaborate to ensure effective and reliable product packaging procedures. At the core of these makers is the structure, which supplies structural integrity and houses the various operating components. The drive system, usually a mix of electric motors and gears, assists in the motion of components, enabling specific operation throughout the packaging cycle.
An additional necessary element is the conveyor system, which carries products via various stages of the product packaging process. This is frequently complemented by sensing units and controls that keep an eye on the position and rate of products, guaranteeing synchronization and minimizing mistakes. The filling system is critical for properly dispensing the best amount of item into plans, whether in liquid, powder, or strong type.
Securing mechanisms, consisting of heat sealants or adhesive applicators, play an essential function in protecting packages, protecting against contamination and prolonging life span. Additionally, classifying systems are essential for giving required item details, guaranteeing conformity with regulations. The control panel, equipped with user-friendly interfaces, enables drivers to take care of machine functions, monitor performance, and make modifications as required, making sure optimum productivity and efficiency in packaging operations.
Typical Upkeep Problems
Reliable procedure of product packaging makers counts greatly on normal upkeep to stop usual concerns that can interfere with manufacturing. Amongst these concerns, mechanical damage is widespread, specifically in parts like motors, conveyors, and seals, which can cause unforeseen downtimes. Additionally, imbalance of parts can cause ineffective procedure, triggering products to be incorrectly packaged or damaged throughout the procedure.
One more common maintenance concern entails the build-up of dust and debris, which can hinder the maker's sensors and moving components. packaging machine repair service. This not only affects efficiency however can likewise pose safety and security dangers. Moreover, lubrication failures can bring about boosted rubbing, leading to overheating and ultimate part failing.
Electric problems, commonly originating from loose links or worn-out circuitry, can interrupt equipment functions, bring about considerable manufacturing delays. Lastly, software program glitches due to incorrect arrangements or out-of-date programs can prevent the device's procedure, necessitating prompt intervention. Resolving these common maintenance problems proactively is vital for ensuring optimal performance and durability of product packaging machinery.
Preventative Maintenance Approaches
Implementing preventative upkeep techniques is crucial for sustaining the efficiency and dependability of packaging makers. These approaches incorporate an organized approach to maintenance, concentrating on the regular evaluation my sources and servicing of equipment to preempt potential failures. By sticking to a set up upkeep program, drivers can recognize damage on parts prior to they cause considerable break downs.
Crucial element of a preventative upkeep approach consist of regular assessments, cleaning, part, and lubrication replacements based on producer suggestions. Using checklists can streamline this procedure, making certain that no necessary tasks are forgotten. Furthermore, preserving exact documents of maintenance tasks help in tracking the device's performance with time, assisting in notified decision-making regarding future upkeep requirements.
Training personnel on the significance of preventative upkeep improves compliance and cultivates a culture of proactive care. Carrying out an anticipating maintenance component, utilizing data analytics and sensing unit technology, can better enhance equipment performance by forecasting failures prior to they occur.
Fixing Strategies
When faced with malfunctions or ineffectiveness in packaging makers, utilizing organized troubleshooting strategies is essential for identifying and fixing problems promptly. The initial action in reliable troubleshooting is to develop a clear understanding of the machine's operational parameters and performance metrics. This involves evaluating the device's specifications, as well as any mistake signals or codes presented.
Following, drivers must carry out a visual evaluation, checking for their website apparent signs of misalignment, damage, or wear. This frequently includes checking out sensing units, gears, and belts to determine possible root causes of breakdown. Gathering functional data, such as production prices and downtime logs, can also give insights into reoccuring problems.
Once possible problems are recognized, making use of a rational strategy to isolate the origin cause is crucial. This might require testing specific elements or systems in a regulated manner. Taking part in conversations with operators that connect with the machinery routinely can generate valuable comments concerning unusual habits or patterns.
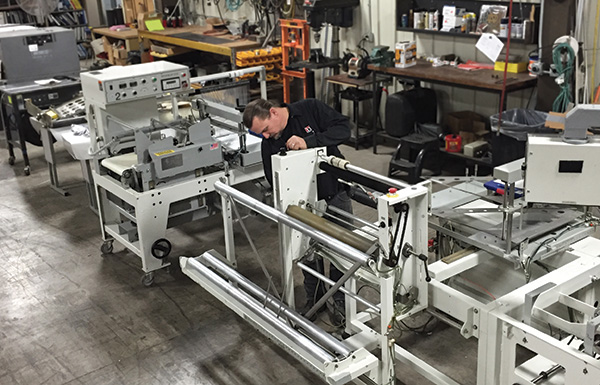
Fixing and Substitute Best Practices
A comprehensive understanding of fixing and substitute best techniques is important for maintaining the long life and efficiency of product packaging makers. Frequently assessing the problem of machine elements enables prompt intervention, protecting against more significant concerns that can cause costly downtimes.
When fixings are required, it is vital to use OEM (Original Devices Maker) components to ensure compatibility and efficiency. This not only preserves the stability of the equipment but likewise promotes guarantee arrangements. Additionally, it is a good idea to maintain an inventory of vital extra components to facilitate quick substitutes and decrease operational disruptions.
For complicated fixings, engaging certified service technicians with specialized training in product packaging equipment is recommended. They possess the experience to diagnose problems precisely visit their website and implement fixings efficiently. Recording all repair work tasks and parts replacements is critical for maintaining a thorough upkeep background, which can help in future troubleshooting.
Last but not least, carrying out a proactive method, consisting of regular examinations and anticipating upkeep methods, boosts the reliability of product packaging devices. By adhering to these finest techniques, companies can make sure ideal maker performance, reduce functional dangers, and prolong equipment life-span.
Verdict
To conclude, a thorough understanding of product packaging equipment components and effective upkeep approaches is important for optimal efficiency. Normal evaluations and making use of OEM parts can dramatically decrease downtime, while a well-documented upkeep history promotes positive care. Using licensed technicians better boosts repair work high quality and reliability. By executing these methods, companies can guarantee the longevity and effectiveness of packaging equipments, ultimately contributing to boosted functional performance and decreased costs.
Effective maintenance of packaging equipments pivots on a comprehensive understanding of their key parts, including the structure, drive system, and sealing devices.Effective operation of product packaging devices counts greatly on routine maintenance to stop common issues that can disrupt production.Applying preventative maintenance techniques is essential for maintaining the efficiency and reliability of packaging makers. Additionally, maintaining precise documents of maintenance activities aids in tracking the device's performance over time, assisting in educated decision-making pertaining to future upkeep demands.

Report this page